ステンレス板金
医療機器や食品装置などをはじめ、ステンレス(SUS)は様々な産業装置の精密板金で使われています。このページではステンレス板金についての基礎知識から加工方法などの技術に関する情報を解説します。
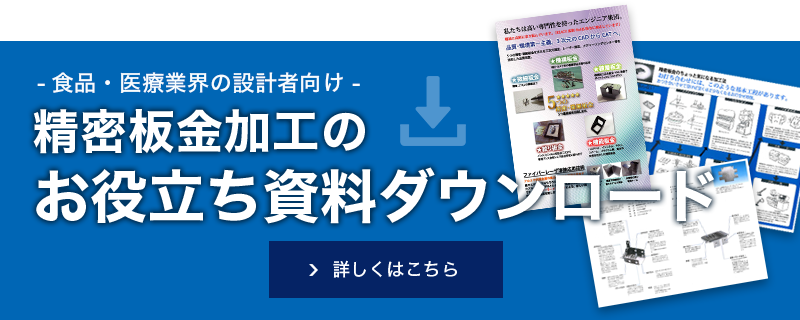
ステンレスとは?
「ステンレス」とは、英語で「さびない」という意味のステンレス鋼です。表面を覆っている不動態皮膜によってさびを防いでいます。しかし、酸性やアルカリ性のものに触れていると、さびる可能性があります。JIS規格のなかだけでも100種類以上の鋼材があり、用途によって使い道はさまざまです。
さびにくい素材として広く使われており、ステンレスは100%リサイクルが可能な素材であることから、環境に及ぼす影響を抑えられる合金としても評価されています。
ステンレス板金とは?
ステンレス板金とは、ステンレスを板状に加工された素材を指します。ステンレス板金は、水や熱に強いため、食品機器や医療機器などに使われています。
ステンレスは熱伝導性が悪く、熱を蓄えやすいため、熱による膨張が大きくなる特性を持ちます。加工性は、展延性に優れるので曲げ加工に向いていますが、旋盤やフライスなど、刃物で削る加工には熱が逃げにくいため、向いていません。
ステンレスに熱を加えて加工すると、温度上昇による寸法変化が生じるため、温度が低下した際に縮むことがあります。ステンレスと鉄を加工する際に使用する工具は同じであっても、刃物の送り速度を変える工夫が必要になります。
ステンレス板金の一般的な板厚と加工限界の関係
一般的に流通されているステンレス板金の一般的な板厚は、以下のとおりです。
SUS304 No.1 | 3.0/4.0/5.0/6.0/7.0/8.0/9.0/10/12(mm) |
---|---|
SUS304 2B | 0.3/0.4/0.5/0.6/0.8/1.0/1.2/1.5/2.0/2.5/3.0/4.0/5.0/6.0(mm) |
SUS304 HL | 0.5/0.6/0.8/1.0/1.2/1.5/2.0(mm) |
SUS304 #400 | 0.8/1.0/1.2/1.5/2.0(mm) |
SUS430 | 0.3/0.5/0.8/1.0/1.2/1.5/2.0/2.5/3.0(mm) |
SUS304 縞板 | 2.5/3.0/3.5/4.5/6.0(mm) |
「SUS304」「SUS430」は、ステンレスを指しています。「SUS」は、ステンレスの英語表記「Steel Use Stainless」の頭文字から取った略語です。また、「SUS」の番号は、材質を分類する数字として定められています。たとえば、300番台は「オーステナイト系」と呼ばれるステンレスで、400番台が「フェライト系」と「マルテンサイト系」になります。
それぞれの違いは、鉄に含まれるクロムやニッケルの成分の有無によってわけられます。300番台のステンレスには、クロムとニッケルが入っているのに対して、400番台ではクロムのみが入っています。一般的な板金加工では、0.5~3mmの板厚が多く使われています。 また、ステンレス板金の板厚によって加工限界があります。たとえば、無理曲げをおこなうと、曲げ加工の際に生じる板の抵抗力により、金型から板がずれて曲げ寸法の狙い値との差ができてしまいます。曲げ寸法の狙い値から差ができると、補正するための手直しが発生するため、時間とコストがかかります。
無理曲げによる寸法ずれを防止するためには、曲げ部の両端に「曲げ逃げ」を追加すると、曲げる際の位置決めが容易になり、加工しやすくなります。結果的に角度のずれを抑制できるため、特に量産品においては、品質の担保に役立つでしょう。
ステンレス板金の加工工程、流れ解説
実際にステンレス板金を加工する工程は、以下の流れになります。
- ・抜き、切断
- ・曲げ加工
- ・溶接
- ・仕上げ
- ・検査
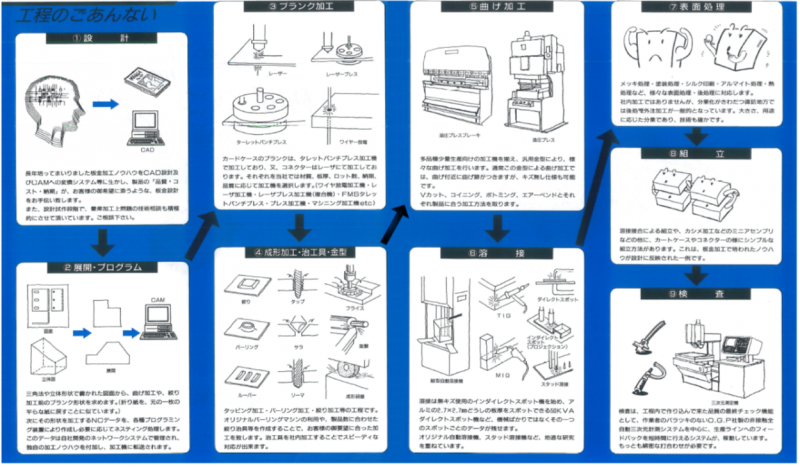
順番に具体的な工程を解説します。
抜き、切断
ステンレス板金の切断と抜きには、上下の刃物で板を挟み込むように切断するシャーリングマシンや所定の位置に打ち抜きを行うタレットパンチが使用されます。後加工のための事前準備として、必要な寸法に応じて加工を行います。最近では、レーザによる切断が主流となり、曲線などの形状でもパンチ金型の制約を受けずに高速で高精度な加工ができるようになりました。
曲げ加工
ステンレスの曲げ加工には、他の素材と比べて工夫が必要になります。ステンレスに力を加えると、若干、元の形状に戻るスプリングバックという現象が強く現れます。曲げ加工の際には、ステンレスの特性を踏まえて、曲げ金型の押し込み量を調整するため、加工圧力が高めになります。
溶接
ステンレス板金の溶接では、レーザ溶接やアーク溶接で他の材料と接合させます。ステンレスには、オーステナイト系やフェライト系といった種類にわけられ、それぞれ溶接に関わる特性が異なります。たとえば、オーステナイト系の場合は、高温割れや変形が発生するため、治具で加工物を固定しながら変形を防止する工夫が行われます。
フェライト系ステンレスでは、熱による焼きが入り、もろくなる特性があり、設計時には注意が必要です。
仕上げ
仕上げは、ステンレスならではのなめらかな表面に仕上げるために必要な工程です。ステンレス板金の仕上げには、グラインダでの研磨や、研磨剤を塗布して円盤工具の高速回転により表面仕上げを行うバフ研磨で鏡面仕上げが行われます。
溶接の焼けを除去したい場合は、上記の研磨除去のほか、部分的に電解研磨で除去する方法があります。
検査
ステンレス板金の仕上げまで完了したあとは、目視による検査や検査機器を使った検査を行います。数量、図面の寸法と角度、公差、表面の仕上がり具合を確認します。検査に合格して初めて製品の組立に進めるため、後戻りのない高精度の加工技術が求められます。
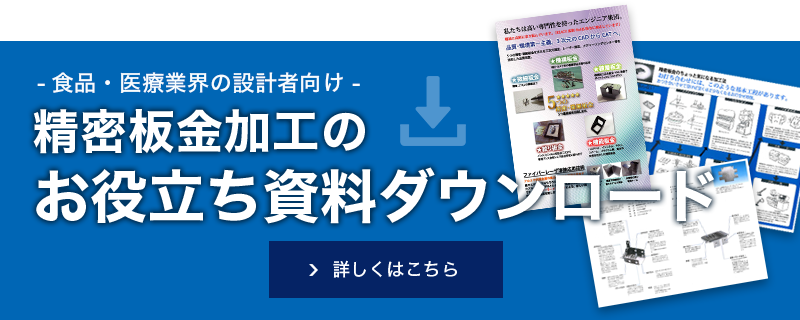
ステンレス板金の抜き・切断加工
ステンレス板金の抜き・切断加工では、断面に沿って平行に反対向きの力を作用させる「せん断」を行います。一般的には、プレスやレーザで加工されますが、特定の形状にせん断するタレットパンチプレスを利用するケースが多くあります。
抜き加工では、必要な部分を抜く「打ち抜き加工」や表面に凹凸を作る「エンボス加工」が施されます。また、切断加工では、レーザ照射による切断を行う「レーザ加工」や3mm以下の板厚に加工する「ステンレス薄板加工」を行います。それぞれの加工方法をメリットとデメリットとともに紹介します。
『レーザ加工』利用シーンや用途
レーザ加工では、レーザの光エネルギーを利用して素材の切断が行われます。レーザ加工のメリットは、歪みの少ない切断面に仕上げられるため、サイズの小さい製品や少量生産に向いています。一方で、レーザ加工を施した製品にわずかなピアス穴ができるデメリットがあります。厚板であるほど、目立ちやすいため、ピアス穴を製品の外側に設けて、製品形状に影響が出ない工夫が必要です。
『エンボス加工』利用シーンや用途
エンボス加工はステンレス板金の表面に凹凸を出すことで素材の強度を高める効果が期待できます。エンボス加工のメリットは、摩擦抵抗が小さくなるため、静電気によるフィルムや紙、食品や錠剤、粉などの貼り付きを抑制することが可能です。 初めからエンボス加工されたエンボス材も市販されています。
『ステンレス薄板加工』利用シーンや用途
ステンレス薄板加工では、板厚が3mm以下の薄板に切削加工やプレス加工を行います。ステンレスの薄板は、医療機器や食品機械に多用され、部品の種類によっては、高精度の仕上がりが求められます。薄板に穴をあける際には、パンチやレーザにより、外形加工と同時に行います。
また、薄板の溶接には、TIG溶接が用いられます。TIG溶接は、1mm以上の薄板を対象に加工が可能ですが、高度な技能を有する作業者が必要で、最近では、その人材不足が懸念されています。TIG溶接のほか、熱の影響を最小限に抑制でき、短期間で習熟できるロボット付きのレーザ溶接機を使用する加工会社も増えてきました。
その他さまざまな板金加工の紹介
精密板金におけるステンレス板金の加工法は、抜き加工、曲げ加工や溶接加工以外にも、以下のような加工方法が存在します。
- ・鏡面加工
- ・タップ加工
- ・リーマ加工
- ・皿穴加工
上記の板金加工について詳しく紹介します。
鏡面加工
ステンレス板金の鏡面仕上げには、バフ研磨や電解研磨が行われます。バフ研磨は一般的に多く使われている方法で、研磨剤を塗布したバフにステンレス板金を押し当てて磨き上げます。一方で、電解研磨とは、電解液に素材を浸して、ごくわずかに表面を溶かすことで鏡面に仕上げる方法です。電解研磨は残留物を残さずに材料表面の凹凸を平滑化でき、光沢による高級感を出せるため、医療分野や食品分野、建築分野で使われる部品の表面処理に採用されています。
タップ加工
タップとは、あらかじめあけた下穴にめねじ形状を作る加工です。タップの加工方法には、切削式と転造式の2種類があります。切削式は、作りたいねじ山に適した下穴をあけて、切削タップを使い、材料を削り落として、ねじ山を作ります。一方で、転造式は、下穴に転造タップで材料に強い力を加えて変形させることで、めねじ形状を作ります。転造式では、切り粉が排出されませんが、ねじ山を作るための高精度な下穴管理が必要です。
リーマ加工
ステンレスは数ある金属のなかでも、穴あけが難しい素材です。また、耐食性に優れている一方で、強度があるので、適切な工具を選定する必要があります。さらに、ステンレスは熱伝導が少ないので、加工すると熱が材料内部にこもりやすい特徴があります。加工時に工具が摩耗するため、作業効率が低下する要因になります。嵌め合い公差穴などの高精度な穴加工が必要な場合は、穴あけの後に、ボール盤を使ってリーマ加工をおこないます。1工程追加になりコストはアップしますが、穴の表面をわずかに削り取り、狙いの寸法に仕上げることができます。
皿穴加工
皿ねじの頭が材料面から出ないようにしたいときに、皿ねじが沈む深さに材料を削り取る皿穴加工をおこないます。ボール盤に面取りカッターを取り付け、ドリル加工のように切削して皿穴を作ります。皿ねじの大きさや沈み深さによって削る深さを微調整することが必要です。
ステンレス板金の溶接ポイント解説、メリット・デメリット、鉄とステンレス溶接の違い
精密板金加工で最も多く使われているステンレス「SUS304」は、錆に強い特性を持ちますが、一般的な溶接材料で加工すると、クロムとニッケルが減少して非常に硬いマルテンサイト組織に変化する可能性があります。マルテンサイト組織に変化すると、硬化や高温割れが発生します。ステンレス板金の溶接の際には、化学成分に配慮した溶接棒の選定が重要になります。
「SUS304」と鉄を溶接する場合は、化学成分と鉄の溶け込み量を小さくすることがポイントです。「SUS309」の溶接棒が推奨されていますが、常温から400℃以上の環境下で割れが生じるケースがあります。ニッケルを主体とした合金の溶接棒であれば、割れのリスクを抑えられますが、低電流・低速度で溶接しなければなりません。
溶接の強度は?
加工性の良さと強度を同時に実現するために、重ねた材料に加圧力と電気を与えて発生した抵抗熱で溶接する抵抗溶接(スポット溶接)が行われます。比較的簡単な作業方法で熟練工でなくても溶接でき、高い強度を実現できるメリットがあります。1打点ごとに素早く溶接できるため、自動車の車体やボディ製造でも使用されています。ただし、鉄とクロムを多く含有されているフェライト系ステンレスの場合は、熱の影響で金属構造が変化するので、加工後の強度が下がります。再度、加熱しても金属構造を変えられない特性を持つため、加工前にテストピースで破壊試験をして強度に対する確認が必要です。
溶接の種類
ステンレス板金におこなう溶接の種類には、おもに「TIG溶接」と「レーザ溶接」があります。「TIG溶接」では、スパッタと呼ばれる溶接時に飛び散って固まる金属の粒が抑えられるため、溶接部を目視確認しながら正確に作業ができるメリットがあります。しかし、シールドガスで溶接部を覆い、酸化から保護しながら溶接するため、風の強い場所ではシールド性に影響が出る可能性があります。
「レーザ溶接」は、ロボットアームの先端にレーザ照射ヘッドが取り付けられ、ティーチングした動きと同時にレーザを照射して溶接します。精密板金加工では、ファイバーレーザやYAGレーザが使われます。ロボットの代わりに人がレーザヘッドを動かして溶接するハンディタイプのレーザ溶接機もあります。
溶接のビードとは?
溶接のビードとは、アーク溶接などで素材を接合した際に、接合部分の表面が凸状に盛り上がっている部分を指します。良質なビードは、銀白色になりますが、金色や青色の場合は溶接不良と判断できます。また、溶接の始点から終点までの一定幅が保たれているビードが理想的です。
よくある溶接物のご紹介
よくある溶接物の事例として、筐体、カバー、蝶番、ナット、ソケット、パイプが代表的です。身近な事例でいえば、機械設備、厨房設備、建築用鉄骨、自転車、車両などが挙げられます。日常生活で使用している製品の多くは、溶接の工程を経て、消費者のもとに届けられています。
溶接トラブル
溶接に欠陥がある場合、製品の安全性に影響を及ぼすため、品質不良の原因になります。よくある欠陥には、高温割れや溶着していない部分が残っているというものがあります。溶接トラブルが発生した場合は、原因の発見と溶接の手順を見直しが必要です。
薄板の場合、材料が変形してしまうため、溶接箇所を剥がして付け直すことが困難です。
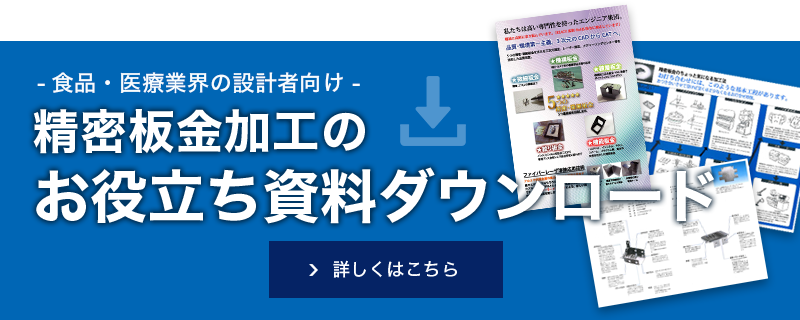
後処理・仕上げ
溶接が完了したら、最後に溶接箇所の仕上げを行います。最初に溶接ビードやバリを除去する作業を行います。次に綺麗な仕上がりにするため、研磨傷を確認しながら面を整えます。必要に応じて、研磨剤とフェルトを使って研磨して鏡面に仕上げます。仕上げの工程では、熟練した技能が求められます。
良い外観とは?ステンレス製品の外観
ステンレス製品において外観は、非常に重要な要素として位置付けられます。材料の違いにより、外観の違いを以下の呼び方で呼んでいます。
No.1 | 銀白色で光沢がない |
---|---|
No.2D | 灰色で光沢が少ない |
No.2B | やや光沢のある仕上げ |
BA | 光沢のある表面仕上げ |
#400 | 鏡面に近い光沢で若干のすじがある |
HL | 連続した研磨目がある仕上げ |
参照:ステンレス協会
ステンレスの外観で気をつけるポイントは、傷を残さずに仕上げを行うことです。ステンレスの材質や板厚によっては、仕上げ後に歪みや変形が生じる場合があります。溶接する段階で傷や歪を最小にして、後の仕上げを少なくする工夫が必要です。
レーザ溶接であれば、きれいで均一なビードで溶接できるため、研磨仕上げをなくせる可能性があり、コストダウンやリードタイム短縮に貢献できます。
ステンレス板金の品質トラブルと対策、対処方法
ステンレスは、鉄と比較すると熱による寸法変化が生じやすい材質であるため、注意が必要です。設計段階から溶接方法に配慮した板厚にする方法も良い方法の1つです。板厚を1mm以上にすると、TIG溶接でも熱による変形を防止できます。
熱歪みによる寸法変化を理解した上で設計しておく必要があります。
溶接割れ
ステンレス板金の溶接割れは、高温割れ、低温割れのいずれかに原因があります。高温割れが発生する要因は、凝固割れと液化割れの2つにわけられます。一般的に結晶粒の粒界で起こるケースが多く、割れ面は酸化が激しくなる特性があります。凝固割れは、溶接した金属が冷却で凝固する際に、収縮応力に耐えきれずに開口してしまう割れのことです。
一方で、液化割れとは、熱部分の結晶粒界にあるニッケルなどの低融点化合物が局部的に溶解することで生じる割れです。
さび(酸化)
ステンレス板金は、鉄と比較すると、錆にくい材料ですが、特定の環境下では錆びる可能性が高まります。おもな錆の原因には、ステンレスの表面が他の金属と接触した状態で放置したときに「もらい錆」が起きます。
他にも、汚れや水分、塩分、強酸、強アルカリが付着すると、錆びてしまいます。ステンレスを錆びさせないためには、表面に汚れがない状態を保ち、他の金属と接着しない場所に保管します。特に傷がついている部分や床と接している部分に錆ができやすいので注意が必要です。
歪み
ステンレス板金に溶接すると、高温による歪みが生じるケースがあります。高温にさらされた金属は、膨張する特性がありますが、自然冷却で縮小されます。しかし、製品の形状や板厚、溶接長さなどの条件によって、歪みが残る場合があります。歪みを防止するためには、加工する素材を治具で固定して歪みを抑え込む方法があります。
また、歪んだ部分をハンマーで叩きながら修正を行う方法もあります。特に、溶接箇所が1か所に集中すると、大きな歪みが発生するので、熱を逃がす工夫が必要です。熱伝導の特性を活かして、素材の下に銅板を敷く、濡らした布で冷却させる、などで放熱しやすくなります。
焼け焦げによる変色
ステンレスを溶接する際に、焼け焦げが生じる場合があります。茶色の焼け焦げは見た目を損ないます。焼け焦げがついてしまった場合は、研削法や酸洗法で除去します。研削法は機械で物理的に研削を行うことで、焼け焦げを除去し、外観を綺麗にします。
変色した部分は、熱で表面が酸化して現れた酸化被膜です。酸化被膜を放置すると、錆の原因になるため、ステンレスの耐食性が低下してしまいます。
酸化被膜を除去するには「電解研磨」を行います。電解研磨では、ステンレスの表面に電解液を浸けます。マイナス極とプラス極の設定を行ったステンレスの間に電気を流して、表面を溶解することで酸化皮膜を除去し、平滑になることで耐食性が向上します。
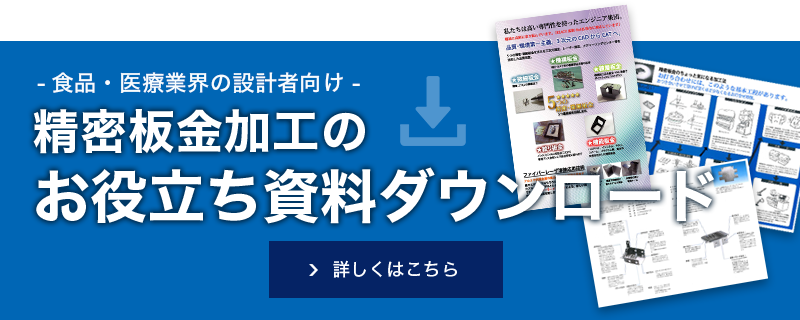